When summer heat hits, comfort isn’t optional—it’s essential. Whether you’re commuting, traveling, or spending time outdoors, the fabric against your skin matters more than ever. For brands and designers, choosing the right material isn’t just about aesthetics—it’s about performance.
That’s where multifunctional summer fabrics come in. These next-gen textiles offer more than just breathability. With built-in moisture-wicking, UV protection, odor control, stretch, and durability, they deliver all-in-one functionality for modern, active lifestyles.
In this article, we’ll break down what makes a fabric truly summer-ready, what features matter most in hot and humid conditions, and why these high-performance fabrics are becoming the go-to for smart apparel brands.
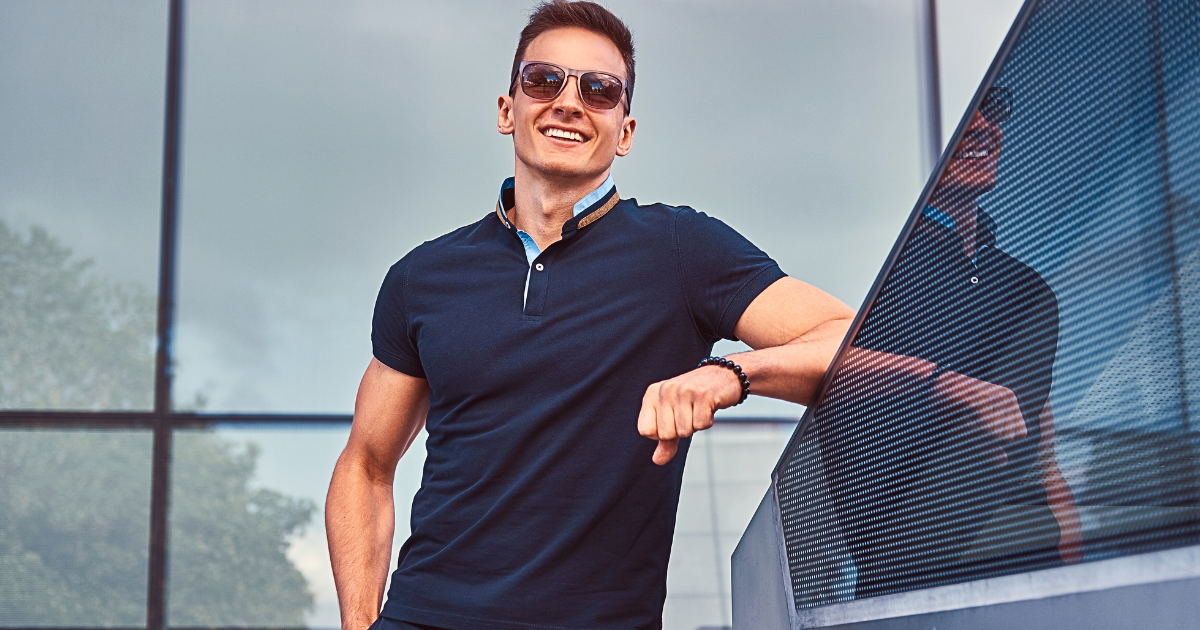
What Makes a Fabric Ideal for Summer?
Lightweight and Breathable Construction
The foundation of any summer-ready fabric is its ability to breathe. Lightweight weaves and open-knit constructions promote airflow, allowing heat to escape and fresh air to circulate. This ventilation helps regulate body temperature and keeps the wearer feeling cool and less restricted—even on the most humid days.
Moisture-Wicking and Fast-Drying Performance
A true summer fabric does more than absorb sweat—it actively pulls moisture away from the skin and accelerates evaporation. This quick-dry feature helps prevent discomfort, skin irritation, and that sticky feeling common in hot, active environments. It’s essential for sportswear, travel wear, and everyday summer outfits.
UV Protection and Odor-Resistant Finishes
Summer often means extended exposure to sunlight, so fabrics with built-in UV protection are crucial for shielding skin from harmful rays. To maintain long-lasting freshness, we integrate silver ion antibacterial technology, which effectively inhibits the growth of odor-causing bacteria. This helps garments stay clean and odor-free even after prolonged wear—making it ideal for hot climates, travel, and active use.
SPORTINGTEX®
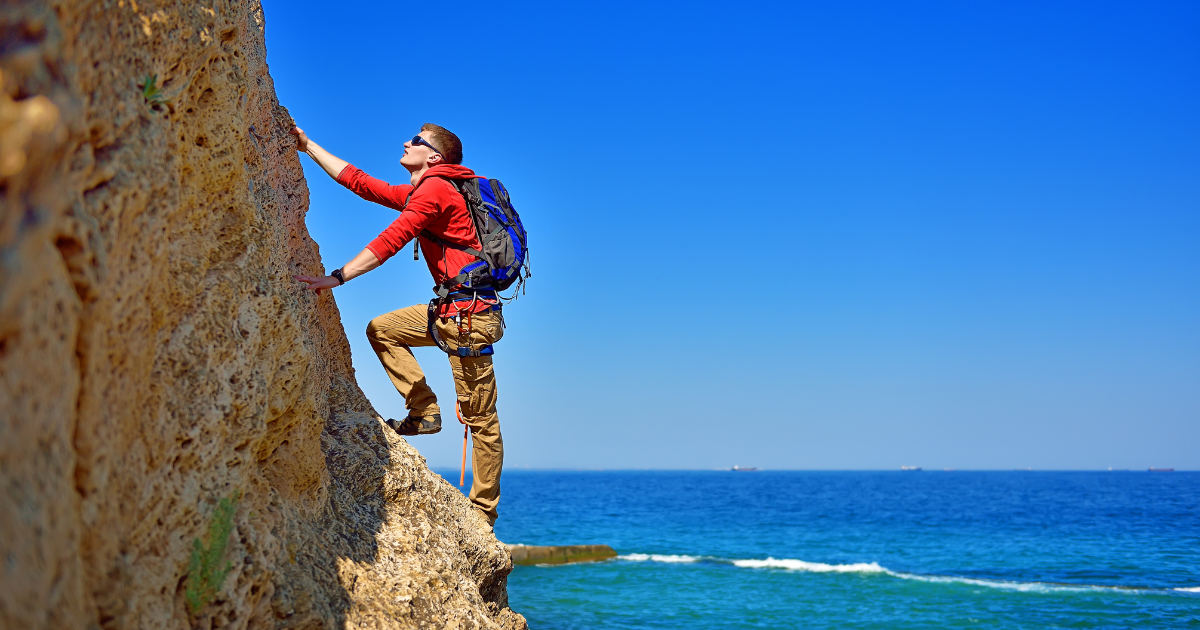
Key Functions of High-Performance Summer Fabrics
Cooling Technology for Heat Management
Modern cooling fabrics are more than just lightweight—they actively help regulate body temperature. Using technologies like cooling minerals, phase-change materials (PCMs), or specially engineered yarns with cross-sectional structures, these fabrics deliver a cool-to-the-touch sensation and provide long-lasting relief in hot conditions. This makes them especially valuable for sportswear, commuter wear, and outdoor clothing.
Antibacterial and Odor-Control Finishes
Sweat isn’t the problem—it’s the bacteria that feed on sweat. That’s why antibacterial treatments, such as silver ion or zinc-based technologies, are integrated into high-performance fabrics to inhibit microbial growth. This not only keeps garments fresher for longer but also reduces the need for frequent washing, extending the fabric’s life and improving hygiene—ideal for humid weather, travel, and all-day wear.
Stretchable and Wrinkle-Resistant Properties
Comfort and appearance go hand in hand. Fabrics with built-in elastane or mechanical stretch move fluidly with the body, while wrinkle-resistant construction helps garments maintain a clean, polished look—even after being packed in a suitcase or worn through a full day. These properties are particularly important for travelwear, office-casual designs, and everyday summer essentials.
Nylon-Spandex Blend: Breathable, Flexible, and Performance-Driven
Lightweight yet exceptionally durable, nylon-spandex blends are a go-to choice for high-performance summer apparel. These fabrics offer excellent breathability, moisture-wicking capabilities, and 4-way stretch—delivering maximum comfort and mobility during workouts, outdoor adventures, or long travel days. Their shape retention and smooth surface also make them ideal for form-fitting designs like leggings, active tops, and athleisure wear.
Polyester Mesh with UV Protection: Lightweight Structure, Maximum Ventilation
Engineered for high-output performance and outdoor exposure, polyester mesh fabrics with integrated UV-blocking treatments offer both durability and protection. Their porous construction promotes airflow, while UV-resistant finishes shield skin from harmful rays—making them ideal for sports uniforms, team apparel, outdoor accessories, and workwear. These fabrics also print well, making them a strong option for branded collections and promotional gear.
SPORTINGTEX®
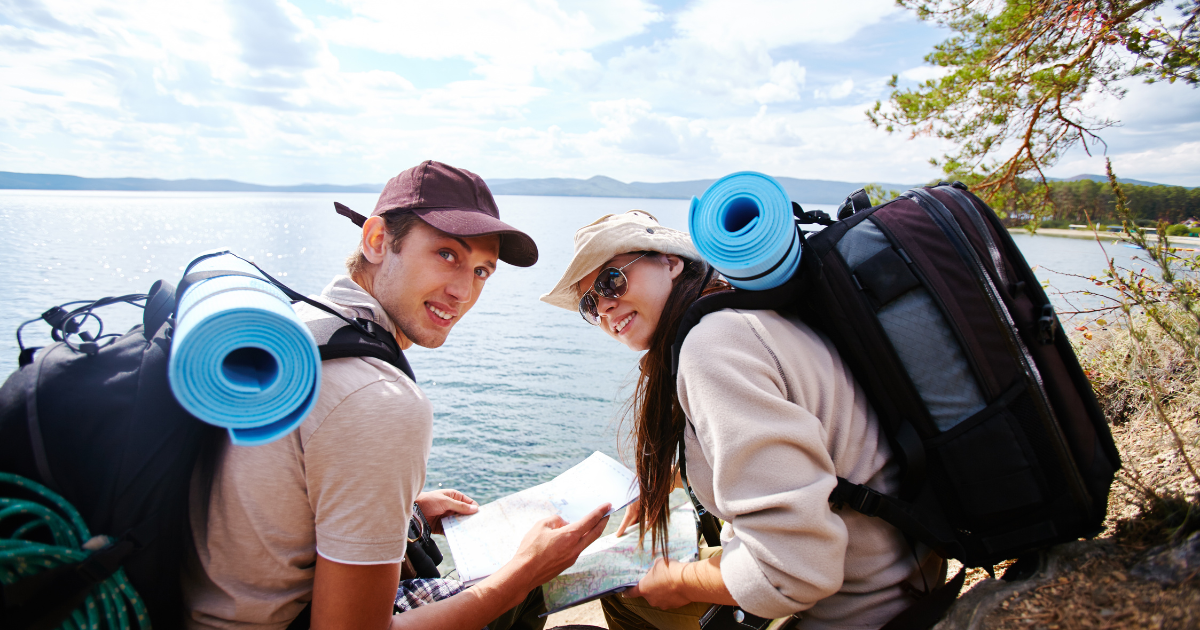
Ideal Applications Across Summer Lifestyles
Activewear and Outdoor Sports
For runners, hikers, cyclists, and fitness enthusiasts, multifunctional fabrics are essential to maintaining performance and comfort. With their moisture-wicking, quick-drying, and odor-resistant features, these fabrics help regulate body temperature and keep wearers feeling dry and fresh—even during high-intensity training or long outdoor sessions.
Travel and Urban Commuter Clothing
Whether navigating a hot city commute or exploring multiple climates in one trip, travelers need clothing that adapts with ease. Fabrics that are quick-dry, wrinkle-resistant, and odor-controlling reduce the need for packing excess items, simplify outfit changes, and stay fresh even after long days. Ideal for shirts, pants, jackets, and base layers that prioritize both function and packability.
Casual Summer Fashion and Loungewear
Multifunctional doesn’t have to mean overly technical. Today’s high-performance fabrics are designed to look and feel like everyday wear—soft, breathable, and stylish. From breezy summer tops and flowy dresses to relaxed loungewear and resort-inspired pieces, these fabrics empower designers to merge comfort, performance, and aesthetic appeal in one garment.
Why Choose Our Fabric Solutions for Summer?
Certified Quality and Sustainable Production
We are committed to delivering fabrics that meet the highest global standards—both in performance and environmental responsibility.
Customizable Finishes and Functional Blends
No two collections are the same—and neither are their fabric needs. We offer fully customizable textile solutionstailored to your specific performance goals. Whether you’re looking for cool-touch finishes, UV protection, silver-ion antibacterial treatment, or a combination of features in one fabric, we can engineer blends that align with your brand identity and end-user expectations.
End-to-End OEM/ODM Support for Global Brands
From sourcing high-performance yarns to final garment production, we provide comprehensive OEM/ODM services for brands worldwide. Our experienced team supports every stage—from prototyping and sampling to mass production—ensuring your summer collections are delivered on time, on spec, and ready for market. Trusted by leading labels across activewear, casualwear, and lifestyle segments, we help turn design ideas into high-function reality.
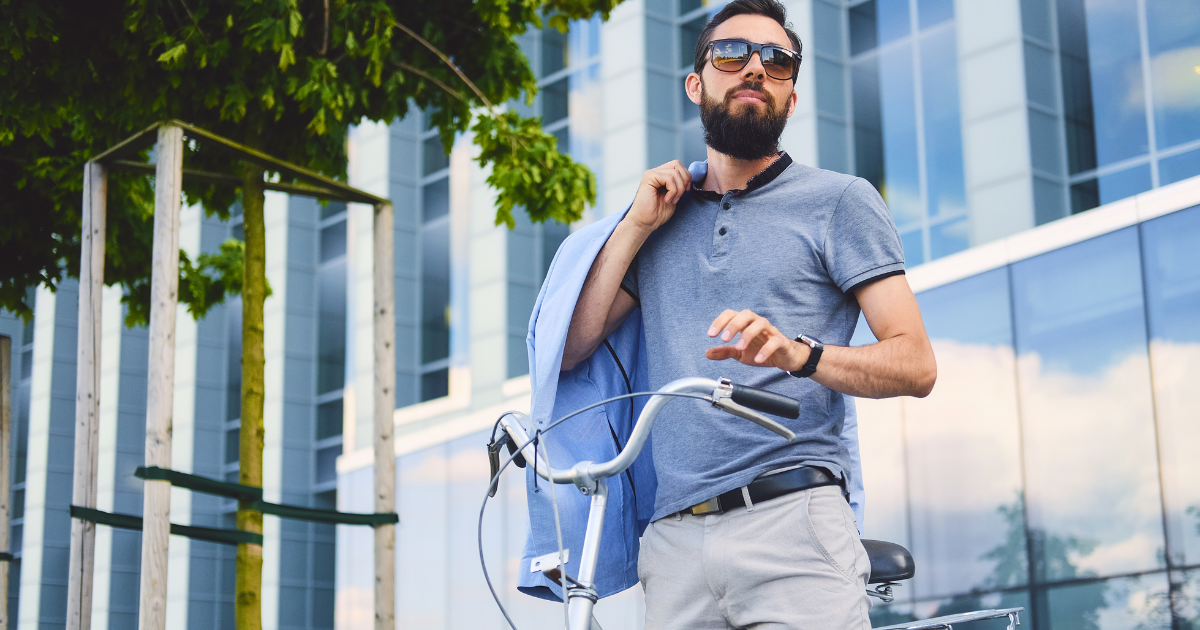
FAQs About Summer Fabrics
Can a fabric be both breathable and UV-resistant?
Absolutely. Thanks to advancements in textile technology, it’s now possible to engineer fabrics that allow airflow while also blocking harmful UV rays. This dual-functionality is perfect for outdoor wear, providing both comfort and protection without adding weight or stiffness.
Is quick-dry fabric also sweat-proof?
Quick-dry fabrics are designed to pull moisture away from the skin and dry rapidly, which helps reduce that sticky, damp feeling. While they may not completely prevent visible sweat marks (especially with lighter-colored or thinner fabrics), they do significantly improve overall comfort and drying speed, making them a top choice for active and summer wear.
Multifunctional summer fabrics are no longer a luxury—they’ve become a necessity for today’s consumers who expect more from what they wear. Comfort, performance, and sustainability are no longer optional—they’re the baseline. If you’re looking to elevate your summer collection with high-performance textiles that deliver on every front,contact us today to explore customized fabric solutions built for real-world needs.